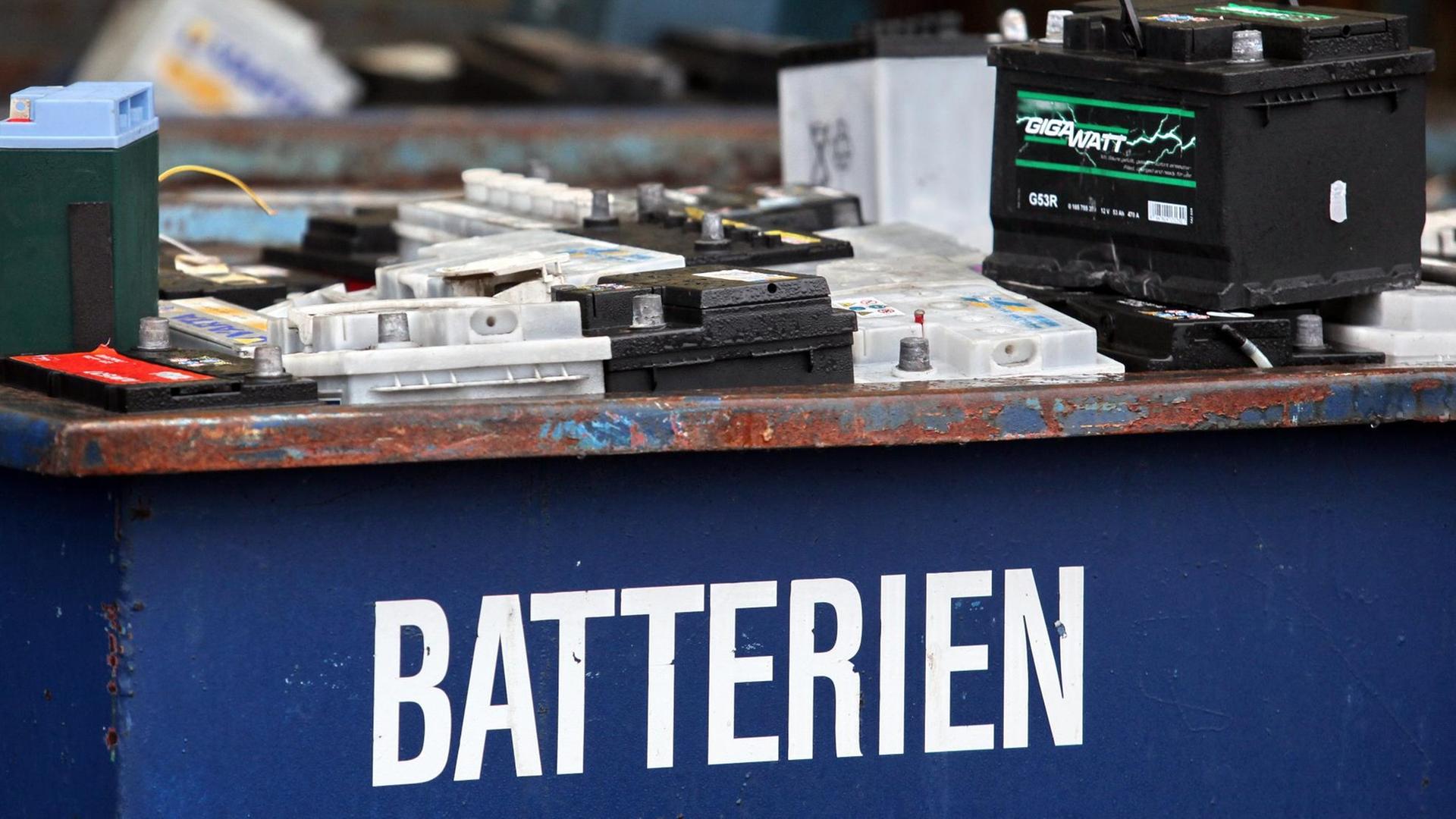
Wie Hängeregale für Akten sehen die Stahlgestelle in der Werkshalle der Firma Hoppecke aus. Darin trocknen orangefarbene und graue Platten. Sie bestehen aus einem Metallgitter, auf das eine Bleipaste aufgebracht wurde. Die Platten sorgen für die chemische Reaktion in Industrie-Bleisäurebatterien – dem Hauptprodukt während der gesamten Firmengeschichte.
1927 hat Carl Zoellner, dessen Familie aus der Metallbranche kam, den Betrieb in Brilon-Hoppecke gegründet. Die NS-Zeit erbrachte einen wirtschaftlichen Aufschwung; auch den Krieg überstanden die Standorte weitgehend unversehrt. Um dem Einsatz von Zwangsarbeitern aus Polen und der Ukraine Rechnung zu tragen, trat Hoppecke 2000 der Bundesstiftung "Erinnerung, Verantwortung, Zukunft" bei und leistete einen sechsstelligen Beitrag.
Bedroht sah sich das Unternehmen Mitte der 90er-Jahre. Die gesamte Branche rutschte in die Krise, sagt der heutige Geschäftsführer Marc Zoellner. Er ist der Urenkel des Firmengründers.
"Während am Anfang der 1990er-Jahre noch über 25 Batteriehersteller in Europa am Markt waren, waren es am Ende nur noch eine Handvoll. Viele sind damals kaputtgegangen oder sind gekauft worden. Und die meisten sind heute in zwei großen amerikanischen Konzernen aufgegangen, während die Firma Hoppecke heute der größte Hersteller von Blei-Akkumulatoren in europäischer Hand ist."
Ärger kann es aber auch bei übersichtlicher Konkurrenz geben. Vor rund zwei Monaten verdonnerte das Bundeskartellamt Hoppecke und einen anderen Batterie-Hersteller aus NRW zu einer millionen-schweren Kartellstrafe. Batterien für die Notstromversorgung und teils auch für Gabelstapler waren ins Visier der Wettbewerbshüter geraten. Nur ein Teilbereich des Gesamtgeschäfts, das auf vier Pfeilern ruht, erklärt Marc Zoellner:
"Emissionsfreier Antrieb von Industriefahrzeugen ist ein wichtiger Bereich. Gabelstapler und Schlepper gehören dazu. Dann geht es um die Speicherung von regenerativen Energien. Der dritte Bereich bezieht sich auf Back-up-Anwendungen. Da geht es dann darum, Netze gegen Ausfall zu sichern oder instabile Netze zu stabilisieren. Und im vierten Bereich geht es um mitfahrende Batterien, die sich um das Energiemanagement in Zügen, gerade in U-Bahnen und Schnellzügen, kümmern".
Lithium-Ionen-Batterien sind in der Industrie zunehmend gefragt. Denn sie halten lange, sind leicht, haben hohe Kapazitäten sowie kurze Auflade- und Abrufzeiten. Marketingleiter Boris Langerbein erläutert, warum die großen und schweren Bleisäure-Batterien trotzdem nicht aus dem Sortiment verschwinden werden:
"Lithium kommt vor allem dann zum Tragen, wenn es um Größe und Gewicht geht. Bei Gabelstaplern ist es zum Beispiel nicht so entscheidend. Denn die brauchen immer ein Gegengewicht. Bei Lithium müssen wir immer Zusatzgewichte mit einbauen. Und wenn ich dann Lithium bei manchen Anwendungen auswählen würde, kommt immer auch eine größere Systemüberwachung hinzu, das bei Blei nicht immer notwendig ist."
Diese Steuerelektronik sorgt dafür, dass die Lithium-Ionen-Akkus kontrolliert aufgeladen und auch wieder entladen werden. Ohne Systemüberwachung bestünde unter Umständen Brandgefahr - was explodierende Handy-Akkus bereits bewiesen haben.
Vorbildlich im Recycling
Gebrauchte Lithium-Ionen-Batterien zu recyceln, ist zudem sehr aufwendig. Die Bestandteile von Bleisäure-Batterien lassen sich aber vollständig wiederverwerten. Hoppecke betreibt dafür seit 1960 eine werkseigene Metallhütte. Europaweit einmalig sei das, lobt sich das Unternehmen. Zuerst wird die Säure aus den Batterien gelassen. Anschließend bricht ein großer Kran-Greifer die Gehäuse auf, sagt Hütten-Geschäftsführer Dieter Henke:
"Die ganzen Batterien, ohne Säure, gehen in eine große Mühle und werden dort zerkleinert. Und nach dem Zerkleinern erfolgt das Trennen auf physikalischem Wege. Blei ist halt eben schwer und schwimmt nicht. Und Kunststoffe sind leichter und schwimmen auf. Ein Schweb-Sink-Verfahren heißt das fachlich richtig."
Das meist recycelte Produkt der Welt
In einem meterhohen Ofen, der einer liegenden Tonne ähnelt, wird das Altblei unter 1000 Grad wieder eingeschmolzen und zu Barren geformt. Bis zu 100 Tonnen Industrie- und Autobatterien verwertet Hoppecke so täglich – und das rund um die Uhr im Dreischicht-Betrieb. Dieter Henke fügt hinzu:
"Bleisäure-Batterien sind das meistrecycelte Produkt auf der Welt. Es werden prozentual mehr Bleisäure-Batterien recycelt als zum Beispiel Glas oder Papier."
Rund 700 Mitarbeiter sind am Stammsitz in Brilon-Hoppecke beschäftigt. Hier befindet sich auch die komplette Betriebsverwaltung. Die restlichen 1.300 Angestellten verteilen sich auf das Zweigwerk in Zwickau – und vor allem auf die Standorte im europäischen Ausland, in den USA und Asien, erklärt Marketingleiter Boris Langerbein:
"Weil der Markt dort stetig wächst - im Bereich der Energieversorgung und auch in der Elektromobilität im Industriebereich. Und wir schiffen jetzt nicht Tonnen Blei durch die Gegend, sondern haben dann vor Ort auch entsprechend ein Werk dafür."
Hoffen auf die nächste Generation
400 Millionen Euro Jahresumsatz kann die Firma Hoppecke aktuell erzielen. Nach 90 Firmenjahren wünscht sich der Urenkel des Firmengründers, dass es weiter geht mit der Familientradition. Drei Kinder hat Marc Zoellner - und eine Hoffnung:
"Wer dann in der Familie da reinkommt, das entscheidet sich erst, wenn Ausbildungen abgeschlossen sind, erste Nachweise erledigt sind und natürlich auch ein Interesse da ist, das zu tun. Aber es ist natürlich ein Wunsch, dass so ein Unternehmen möglichst von der vierten in die fünfte Generation weitergeht."