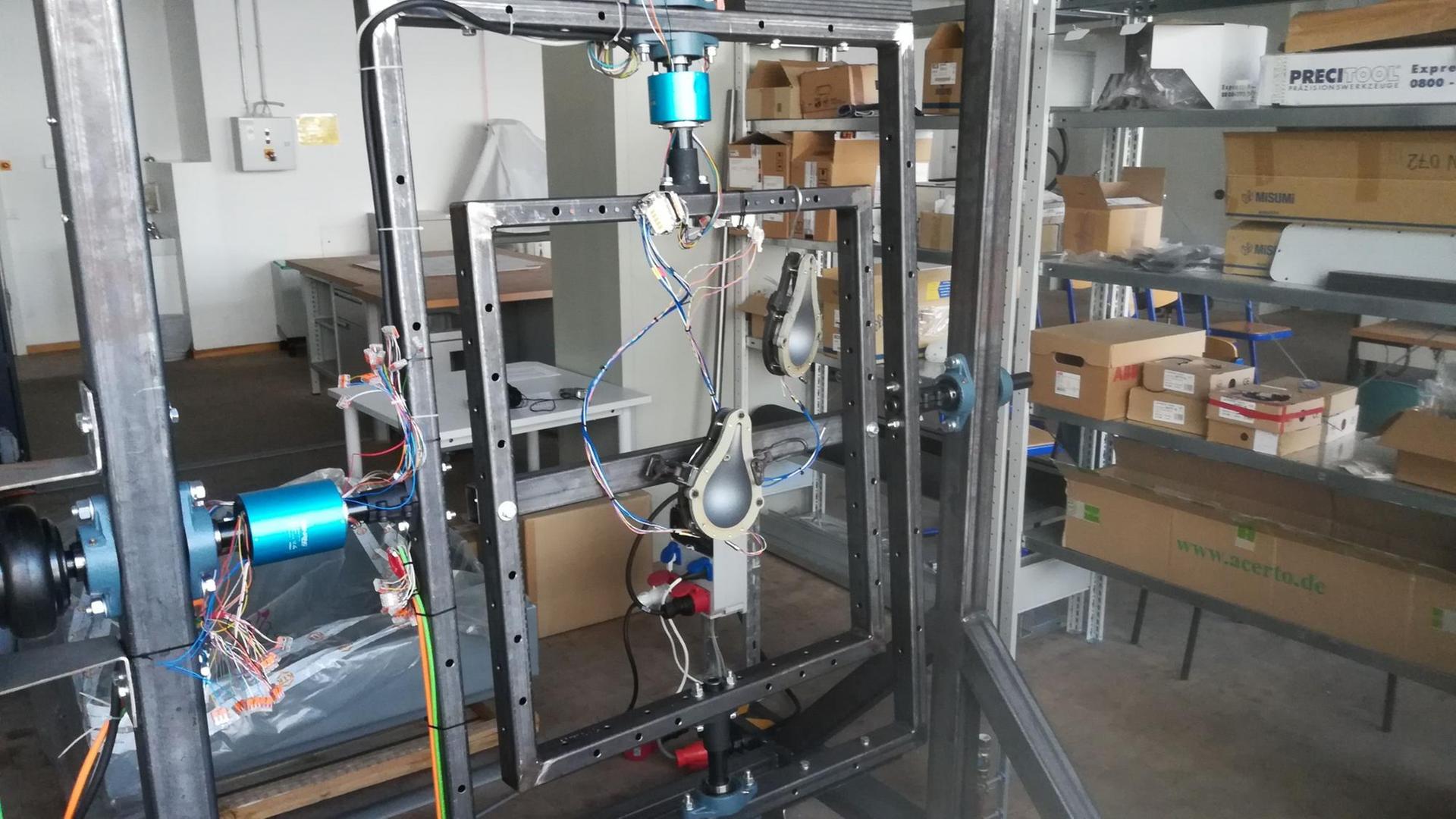
Fast tänzerisch wirkt es, wenn die Rotationsguss-Maschine in der Leipziger Hochschule für Technik, Wirtschaft und Kultur läuft. Ein etwa zwei Meter mal zwei Meter großer Stahlrahmen dreht sich senkrecht wie ein Wasserrad, während in seiner Mitte ein zweiter, waagerecht rotierender Rahmen befestigt ist. Im inneren Rahmen hängt eine tropfenartige Metallform. Dort lässt sich Polyethylen-Kunststoff einfüllen und durch Erhitzen verflüssigen.
Die Form wird durch die Maschine beinahe lautlos in alle Richtungen gedreht. Somit lagert sich der Kunststoff an den Wänden ab und härtet zu Lampenschirmen aus, erklärt Prof. Dr. Fritz-Peter Schulze vom Institut für Maschinenbau:
"Die werden von innen beleuchtet, naturgemäß. Da sieht man jede Unregelmäßigkeit in der Wandstärke beispielsweise. Allerdings zeigen sich auch Fehler, wie beispielsweise Schwärzungen, extrem deutlich".
Wie bei der Herstellung von Schokoladenfiguren
Meistens entstehen etwa Wassertanks oder Kinderspielzeuge per Rotationsguss. Dort sind kleine Materialfehler vertretbar, nicht aber bei Designer-Deckenleuchten. Der Kölner Lichtdesigner Thomas Schulte bat die Leipziger Forscher deshalb darum, eine spezielle Rotationsgussmaschine zu entwickeln.
Anfangen mussten sie bei der Heizmethode, erläutert Hans-Martin Dörfler, Mitarbeiter am Institut. Konventionelle Maschinen arbeiten mit einem simplen Verfahren:
"Diese ganze Rotationsvorrichtung mit der Form, die schwenkt quasi in so einen Gasofen ein. Da sind unten Gasbrenner drin und die heizen einfach diesen Raum auf und geben die Wärme an die Form ab."
Ungewollte Verunreinigungen und Unregelmäßigkeiten
Das Problem an der Technik ist aber: Beim Befüllen können Rußpartikel mit in die Form gelangen, die Schwärzungen verursachen. Außerdem heizen die Formen nicht immer gleichmäßig auf, wodurch ebenfalls sichtbare Gussfehler entstehen. Die Forscher bauten deshalb eine teflonbeschichtete Form, bestückt mit aufwändiger Technik.
"Jede Formhälfte, da ist ein Heizelement integriert. Und in jeder Formhälfte haben wir an zwei Punkten einen Temperatursensor. In Echtzeit wird da die Temperatur gemessen und das geht in die Regelung mit ein."
So kann man die Form kontrolliert und rußfrei auf 200 Grad Celsius aufheizen, das ist die optimale Schmelztemperatur für das Granulat. Die Steuerelektronik regelt aber nicht nur die Heiztemperatur, sondern auch die sogenannten Rotationspfade - also die Abfolge der Richtungen, in die die Form gedreht wird. Bisher rotieren vertikale und horizontale Achse immer gleich – nicht so bei der Leipziger Anlage, erläutert Fritz-Peter Schulze:
"Wenn man die Rotationspfade ungeplant darstellt, dann könnten sich Schleier bilden. Unser Rotierer arbeitet nach einem bestimmten Schema, das hält sich an die Geometrie des Bauteils."
Dadurch verteilt sich der flüssige Kunststoff sehr gleichmäßig zu einer etwa zwei Millimeter dicken Schicht. Außerdem galt es, die optimale Rotationszeit für fehlerfreie Leuchten zu ermitteln.
"Zu lang ist unwirtschaftlich, zu kurz bedeutet, das Granulat wird nicht vollständig aufgeschmolzen. Das heißt, es bildet sich an der Wand innen immer noch eine Granulat-Anhaftung – und die sieht man dann in der Lampe."
Mehr Lampenschirme und weniger Materialfehler
Mit dem neuen Verfahren entstehen weitgehend fehlerfreie Produkte – im Vergleich zur konventionellen Methode. Sie hat den Kölner Leuchtendesigner schon viel Ärger bereitet, weiß Hans-Martin Dörfler:
"Im Endeffekt ging es sogar so weit, dass die Hersteller die Aufträge einfach nicht mehr angenommen haben und gesagt haben: 'Wir haben hier Ausschuss von 80 Prozent, das lohnt sich nicht für uns'. Sie hatten am Ende wirklich Schwierigkeiten, eine Firma zu finden, die für sie die Lampenschirme in der Qualität herstellt, wie sie sie brauchen."
Demnächst soll die Rotationsguss-Anlage von Leipzig zu Leuchtendesigner Thomas Schulte nach Köln umziehen. Der kann dann zum Beispiel bis zu sieben Lampenschirme gleichzeitig herstellen – bei gut 85 Prozent Energieersparnis und fast ohne Materialfehler.