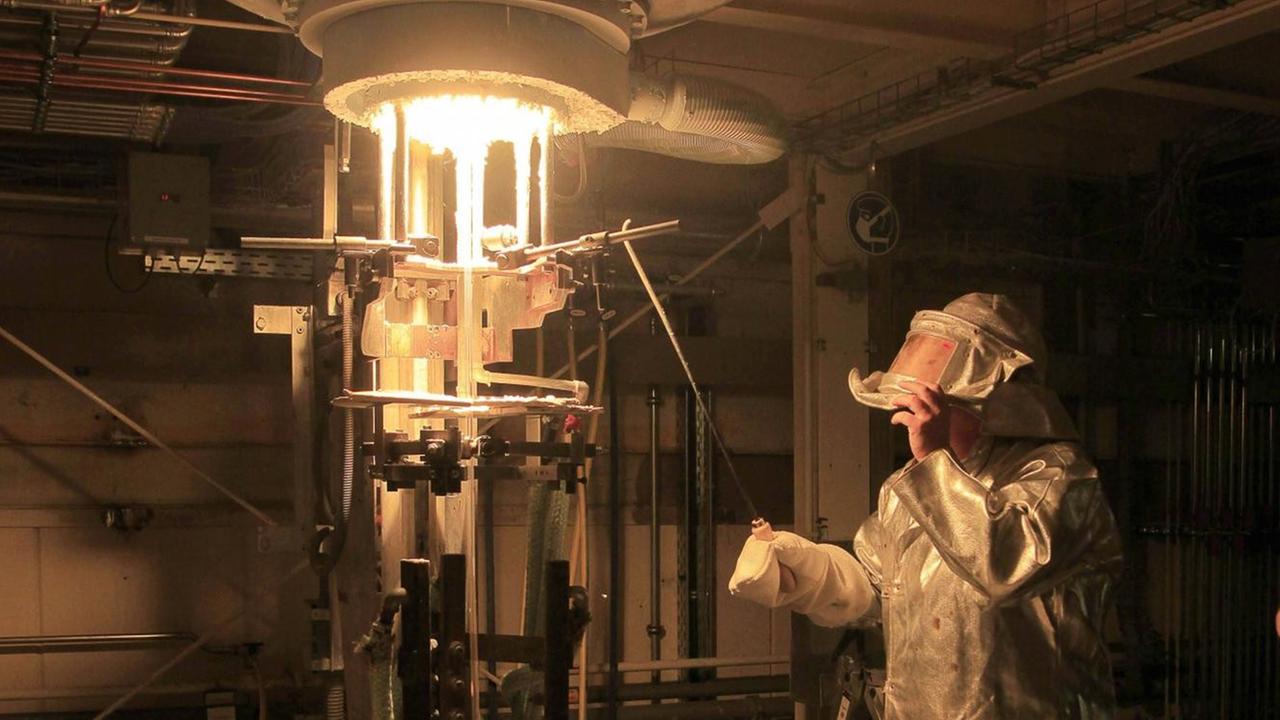
Glas ist ein faszinierendes Material. Hart, lange haltbar, chemisch sehr stabil, luftdicht und wasserfest, durchsichtig, mit sehr guten optischen Eigenschaften. Doch in vielen Anwendungsbereichen haben heute Kunststoffe Glas den Rang abgelaufen. Das liege vor allem an der viel einfacheren und schnelleren Verarbeitung, sagt der Materialforscher Frederik Kotz.
"Also Spritzguss ist der Grund, warum sich Kunststoffe in der Massen-Technologie vor allem durchgesetzt haben."
Beim Spritzguss wird ein Kunststoff-Rohmaterial über seinen Schmelzpunkt von wenigen hundert Grad erhitzt und dann als pastöse Masse unter hohem Druck in metallene Formen gegossen. Nach einer kurzen Abkühlungsphase ist das Werkstück ausgehärtet und der nächste Spritzgussvorgang kann beginnen – mitunter im Takt weniger Sekunden. Die Glasverformung erfordert hingegen Temperaturen von 1400 bis 2000 Grad Celsius. Strukturen müssen energie- und zeitaufwendig gezogen und geblasen werden. Vom Spritzgießen konnten Glastechniker bisher nur träumen. Doch der Traum wird jetzt Realität.
Spritzguss bringt Glas in jede beliebige Form
"Wir können klassischen Kunststoffspritzguss einsetzen. Das heißt, wir machen das Ganze bei 130 Grad."
Frederik Kotz hat mit seinem Team am Materialforschungszentrum der Universität Freiburg eine Technik entwickelt, wie man Objekte auch aus Glas spritzgießen kann. Der Clou dabei ist das Ausgangsmaterial: Pellets aus einer speziellen Kunststoffmischung, in deren Matrix sehr fein gemahlenes Glaspulver enthalten ist. Der Glasanteil in diesen Komposit-Materialien macht bis zu 60 Prozent des Volumens aus. Frederik Kotz nennt sie deshalb nicht mehr Polymere sondern Glassomere.
"Die Glassomere kann man wie einen klassischen Kunststoff mit einer Kunststoff- Spritzgussmaschine verarbeiten. Mit den gleichen Durchsätzen, mit den gleichen Formeneinsätzen. Das heißt, man braucht kein Spezial-Equipment. Erst nach der Formgebung kommt das Bauteil in den Ofen und wird in Glas umgewandelt."
De facto folgen nach dem Spritzgießen noch drei Arbeitsschritte. Zuerst kommen die Glas-Spritzgussteile in ein Wasserbad, wo ein großer Teil der Kunststoffe einfach ausgewaschen wird. Sie lassen sich sogar wiederverwenden. Anschließend werden die Formteile auf 600 Grad Celsius erhitzt, um die restlichen Binder-Polymere thermisch zu zersetzen. Am Ende wird das verbliebene, vorgeformte Glaspulver bei 1300 Grad Celsius im Ofen noch zu festem, reinen Glas verbacken, oder in der Fachsprache gesagt: gesintert. Ohne die Polymere als Füllmaterial schrumpfen die Bauteile natürlich ein wenig, aber sie behalten die gewünschte Form.
"Der Schrumpf ist isotrop, das heißt in alle Richtungen gleich. Und da wir die volle Dichte am Schluss erreichen, hängt der Schrumpf nur vom Pulverfüllgrad ab. Das heißt, wir haben maximal einen Füllgrad von 60 Volumenprozent Siliziumdioxid in unseren Mischungen. Das kann man dann ganz genau berechnen, da kommt 15,6 Prozent linearer Schrumpf heraus."
Mikro-Optiken für Smartphone-Kameras
Das Glaspulver in den Glassomeren besteht aus Nanopartikeln in einer Größenordnung von 50 Nanometern. Die feinsten Strukturen, die sich damit realisieren lassen, liegen im Bereich von 500 Nanometern bis einem Mikrometer. Größer geht natürlich immer, doch auch da gibt das Verfahren Grenzen vor. Zum Beispiel wird es ab Wandstärken von mehr als einem Zentimeter sehr schwer, die Kunststoff-Matrix noch auszubrennen.
Die ersten Glassomer-Produkte könnten schon im kommenden Jahr in die Spritzguss-Massenproduktion gehen. Ein sehr großes Potenzial sieht Frederik Kotz zum Beispiel bei optischen Bauteilen für Smartphone-Kameras.
"Also wir haben ein großes Interesse aus dem Bereich Optik, Linsenelemente, komplexe Mikro-Optiken, die man in Kunststoffen schon sehr, sehr einfach herstellen kann. In Gläsern ist es einfach sehr sehr teuer im Moment."
Ein weiteres Einsatzfeld wären Beleuchtungs-Optiken. Die werden heute gerne aus Kunststoff hergestellt, doch sie altern schnell und müssen dann nach drei, vier Jahren ausgetauscht werden. Frederik Kotz spricht von einer Win-Win-Situation, wenn man solche Komponenten durch haltbares Spritzguss-Glas ersetzt.