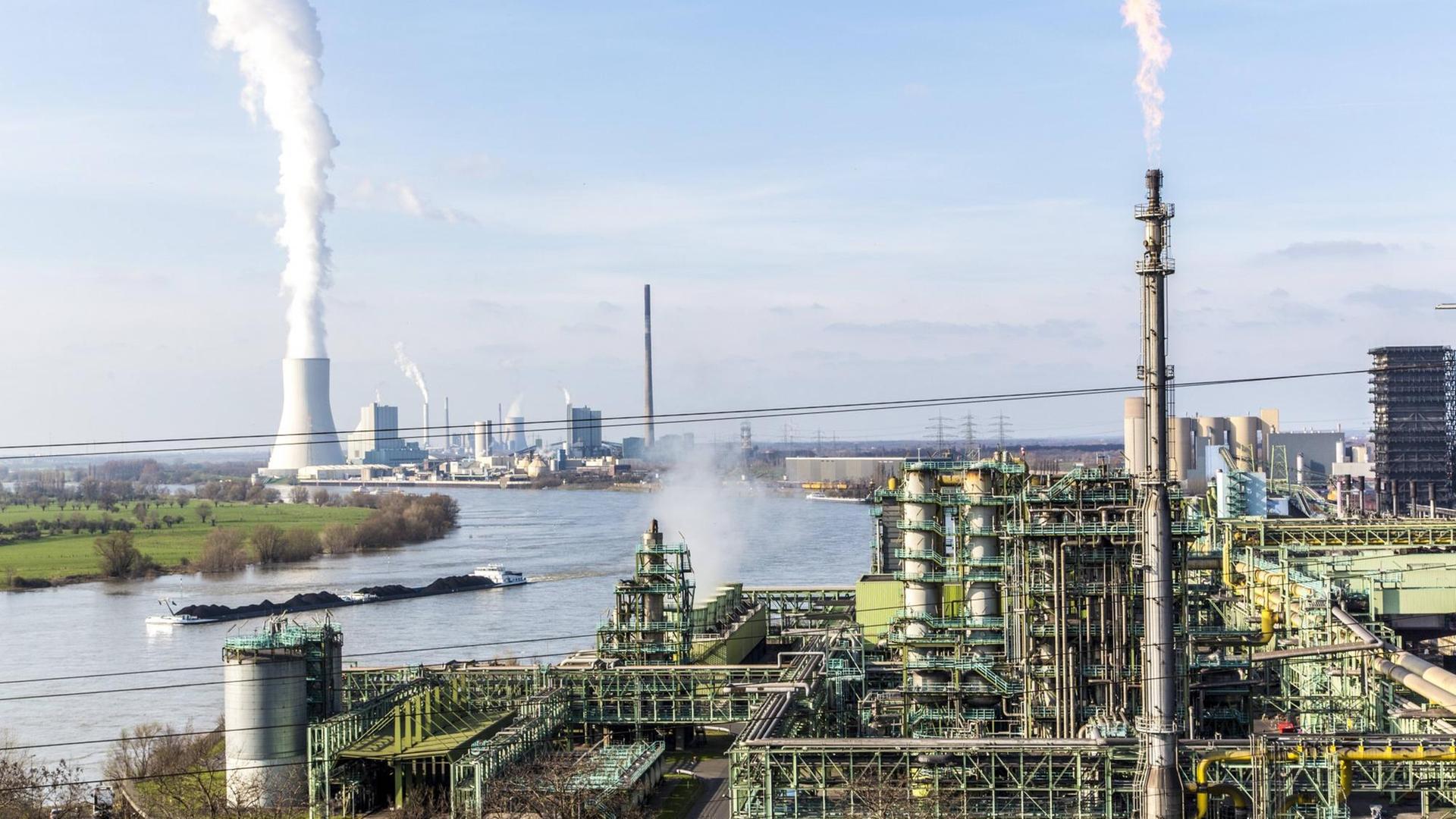
Auf dem Werksgelände von ThyssenKrupp in Duisburg werden nicht nur mehrere Millionen Tonnen Stahl im Jahr hergestellt. Hier befindet sich auch Deutschlands größte Kokerei. Seit gut fünf Jahren sind die Prozessgase der Anlage Gegenstand eines besonderen Forschungsprojektes.
"Wir wollten ursprünglich Düngemittel machen, also Urea, einen sticktsoffbasierten Dünger. In den Prozessgasen sind Ammoniak und CO2 enthalten. Dann haben wir uns die Inhaltsstoffe angeguckt und uns gesagt, es ist vielleicht einfacher, Ammoniumbikarbonat, umgangssprachlich Hirschhornsalz, herzustellen. Dies kann auch als Düngemittel eingesetzt werden oder als Backpulver," erklärt Holger Thielert von ThyssenKrupp. 5,7 Millionen Tonnen Hirschhornsalz werden weltweit pro Jahr produziert. Besonders in fernöstlichen Ländern ist es ein beliebtes Düngemittel.
Eine Versuchsapparatur zur Gewinnung von Hirschhornsalz konnte ThyssenKrupp gemeinsam mit Studierenden der Technischen Universität Berlin entwickeln. Die Maschine zapft die abgehende Pipeline der sogenannten Desorber an. In den drei zylinderförmigen Anlagen wird das zur Abgasreinigung genutzte Wasser von seinen Gasanteilen getrennt, erläutert Peter Liszio, Geschäftsführer der Kokerei.
"Das Wasser, das unten herauskommt, ist heiß, aber so rein, dass es jetzt zur kommunalen Kläranlage gepumpt wird. Am Kopf hingegen gibt es jetzt ganz stark angereichert diese Gase, die bestehen aus Schwefelwasserstoff, aus CO2 und vor allen Dingen aus Ammoniak. Und wenn man Ammoniak und CO2 geschickt zueinander bringt, dann entsteht ein neuer Stoff, das sagenumwobene Hirschhornsalz."
Circa sieben Meter hoch und fünf mal 15 Meter breit ist die Hirschhornsalz-Gewinnungsanlage. Zwischen den riesigen Hochöfen, Pipelines und Röhren wirkt sie damit eher unscheinbar.
CO2-Abgasströme der Hütte anzapfen?
Die Maschine kann rund 70 Prozent der anfallenden Kokerei-Prozessgase verarbeiten. Die restlichen 30 Prozent sind Schwefelwasserstoff und gelangen in eine Entschwefelungsanlage. Bis aber aus Ammoniak, Wasser und CO2 tatsächlich das gewünschte Hirschhornsalz entstand, war es ein langer Weg, sagt Sebastian Riethof, Wissenschaftler an der Technischen Universität Berlin:
"Man muss diese drei Komponenten irgendwie zur Reaktion bringen. Nach dem Stand der Technik wird es halt so gemacht, dass Ammoniakwasser CO2-verpresst wird und unter Druck stehen gelassen wird. Bei uns ist es so, wir mussten halt herausfinden, wie wir aus einem kontinuierlichen Gasstrom diesen Prozess in einem kontinuierlichen Prozess entwickeln."
Lange Versuchsreihen im Labor führten zur folgenden Verarbeitungsmethode: Die Maschine kühlt den Gasstrom zunächst herunter, wodurch der Wasseranteil kondensiert und Ammoniak sowie Kohlendioxid gebunden werden.
"Wir müssen nur darauf achten, dass wir das Ammoniak-CO2-Verhältnis richtig einstellen. Dementsprechend muss halt CO2 zudosiert werden, weil das Ammoniak deutlich im Überschuss entsteht."
Das Kohlendioxid dafür wäre aber leicht zu beschaffen, weiß Peter Liszio:
"Es gibt bahnbrechende Ideen, eventuell die CO2-Abgasströme der Hütte später mal anzuzapfen. Für die Produktion von Ammoniumbikarbonat könnte man das klimaschädliche Gas auswaschen und hier wieder in ein verkaufsfähiges, marktfähiges Produkt einbringen."
"Jeder Kokerei der Welt wäre für diese Anlage tauglich"
Das Gemisch aus Wasser, Ammoniak und CO2 zirkuliert so lange in der Anlage, bis es eine gewisse Konzentration erreicht hat. Das entstandene Salz darin wird schließlich mit einer Zentrifuge ausgeschleudert. 13 Kilogramm Hirschhornsalz lassen sich so stündlich mit der Versuchsanlage in Duisburg herstellen. In den nächsten Monaten möchte das Forscherteam noch einige technische Details optimieren. In zehnfacher Größe gebaut, könnte die Maschine dann bis zu 50.000 Tonnen Hirschhornsalz jährlich produzieren. Damit wäre sie dann für viele Kunden interessant, meint Holger Thielert:
"Man beeinträchtigt gar nicht den normalen Betrieb, sondern nimmt einfach einen Gasstrom aus der Kokerei, behandelt ihn und gibt den Rest wieder zurück in den Prozess, sodass jede Kokerei der Welt für diese Anlage tauglich wäre."