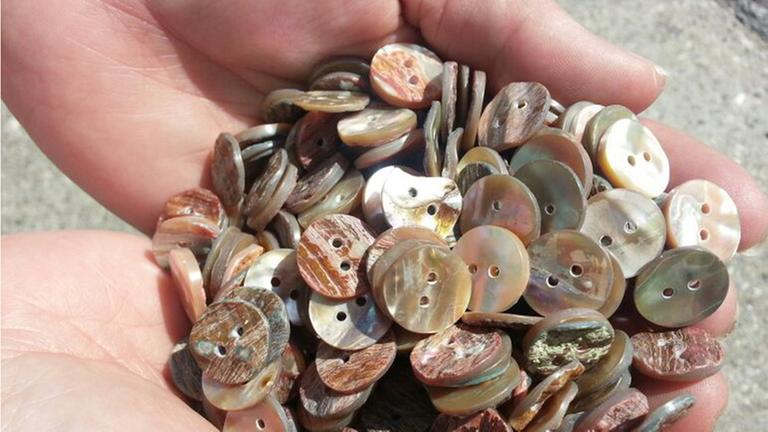
Wurden noch in der Mitte des vergangenen Jahrhunderts hochwertige Knöpfe überwiegend aus Naturmaterialien mehr oder weniger in Handarbeit gefertigt, traf die Betriebe fast über Nacht die Moderne: das Kunststoffzeitalter brach an, und damit kam der Garaus für die meisten handwerklichen Knopfhersteller.
"Bis in die 60er-, 70er-Jahre hat´s 98 Betriebe in Österreich gegeben, die dasselbe gemacht haben, was wir auch heute noch machen, und zwar Knöpfe produziert."
Traditionsbetrieb in fünfter Generation
Genauer gesagt: Perlmuttknöpfe. Der 41-jährige Rainer Mattejka ist der letzte Hersteller in Österreich und einer von vielleicht noch einem Dutzend in ganz Westeuropa, die meist die Haute Couture beliefern. Ein Traditionsbetrieb in fünfter Generation. Sein Ururgroßvater, Rudolf Marchart, hatte die Firma 1911 in Felling im reizvollen, hügeligen Weinviertel gegründet, nur wenige Steinwürfe entfernt vom heutigen Tschechien. Die Grenzflüsse Thaya und March lieferten das schimmernde Rohmaterial für die Drechslerei: Flussmuscheln. Lange arbeitete das Unternehmen damit auskömmlich. Dann
"hat das begonnen mit dem Polyesterknopf, mit dem Kunststoffknopf. Das ist von heute auf morgen eigentlich der Boom gewesen. Und mein Großvater hat von 42 Leuten auf einen Ein-Mann-Betrieb innerhalb von drei, vier Jahren abbauen müssen."
Der Großvater zeigte Durchhaltewillen, ebenso wie zuvor schon dessen Vater, der wegen der allmählich erschöpften Muschelbestände in den heimischen Flüssen in Schwierigkeiten geraten war.
"Mein Urgroßvater hatte das Glück, das war in den 60er-Jahren, bevor eigentlich die vielen Betriebe zugesperrt haben, dass er ein Marchmuschellager von circa 40 Tonnen kaufen konnte. Wir haben noch nichts importieren dürfen. Er hat ungefähr drei Jahre damit arbeiten können, und ab diesem Zeitpunkt dann hat er auch importieren dürfen."
Makassar-Muscheln und Trocas-Schnecken aus Indonesien
Jetzt bezieht die Schleiferei ihr edles Rohmaterial, vor allem Makassar-Muscheln und Trocas-Schnecken, von Perlenzuchtbetrieben meist aus Indonesien, Australien und Neuseeland. 20 Tonnen pro Jahr. Mattejka stellt mit drei Mitarbeitern rund sieben Millionen Knöpfe jährlich her und erwirtschaftet so einen Umsatz von gut einer halben Million Euro. In etwa die gleiche Summe verbuchen drei weitere Beschäftigte in seinem Shop für Schmuck und anderes Exquisites aus Perlmutt.
Von Glamour ist in der Produktionshalle mit den vielen Maschinen nichts zu spüren. Laut arbeiten die Ventilatoren der Absauganlage gegen den Bohr- und Schleifstaub und sorgen für ständiges Rauschen. Vollautomatisch geht hier fast nichts. Knopfherstellung ist in weiten Teilen monotone Handarbeit. Der Aufwand hat seinen Preis: Im Vergleich zum Polyesterprodukt ist Perlmutt zehnmal teurer.
"Ausgebohrt werden die Knopfrondellen mit Diamanthohlbohrern. Und pro Drücken wird eine Rondelle ausgebohrt, pro Tag etwa 13.000 Stück, das heißt 13.000 Mal diesen Hebel hinunterdrücken.
Perlmutt zehnmal teurer als Polyesterprodukt
Geduld und Kraft braucht´s. 150 bis 220 Rohlinge für Hemdknöpfe lassen sich aus einer Makassar-Muschel, Stückpreis etwa zehn Euro, herausholen.
Im nächsten Arbeitsschritt werden die Scheiben geschliffen und auf die gewünschte Stärke gebracht. In einer weiteren Maschine folgt das Drechseln der Façon, des Knopfrands, bevor das Stück die Löcher vom Drillbohrer erhält.
"Einen Knopf muss man ungefähr zwischen acht und zwölf Mal in die Hand nehmen."
Mit der speziell für die Fertigung größerer Produktmengen vor fünf Jahren angeschafften Lasermaschine ist nun das Hin und Her geringer, gesteht der 41-Jährige. Die Maschine, die mit den Rohlingen gefüttert wird und die Arbeitsschritte bis zum Bohren der Löcher und Lasern der Fadenrille automatisch durchführt, war auch nötig, um die Präzisionsvorgaben der Modehäuser erfüllen zu können.
"Hier werden jetzt die Knöpfe in die neue Lasermaschine hineingeschoben. Und wie man genau sieht, wird zuerst die Rückseite der Knopfrondelle verarbeitet. Dieses Material der Schnecken müssen mit der Hand eingeschoben werden, weil sie auf der Rückseite eine Rinde haben. Wenn aber beide Seiten ohne Rinde wären, dann kann man einen Trichter hinaufgeben. Da wird die Rückseite verarbeitet, die Vorderseite, hier sieht man, wie gelasert wird, da werden sie gebohrt. Und hier ist jetzt der fertige Knopf mit dem Rand, zwei Löcher und der Laserung in der Mitte, und auf der Rückseite ist er abgerundet."
Wieder zurück an einem ruhigeren Ort kommentiert der Firmenchef:
"Bevor wir diese Maschine hatten, haben wir ungefähr pro Tag 15.000 Stück Knöpfe produziert, und heute sein mir ungefähr bei 50.000 Stück."
Zumal nun auch Rohlinge in Südostasien geordert werden. Zum Finish geht´s für die Knöpfe in den Raum, in dem sie ihre Strahlkraft erhalten:
"Wir sagen: in das Säurekammerl."
Knöpfe werden hier auf Kundenwunsch eingefärbt, zudem startet hier der Poliervorgang in Trommeln mit Bimsmehl und Wasser. Danach steht ein Bad in schwacher Schwefelsäure an, bevor die Knöpfe über Nacht in einer rotierenden Holztrommel von Millionen Buchenholzwürfelchen auf Hochglanz poliert werden.
Abschließend das Ausrütteln. Die Linsen- bis 2-Euro-Münzen großen Knöpfe, rund oder rechteckig, werden von den Würfeln getrennt. Je nach Ausgangsmaterial schillern nun die Naturschönheiten einfarbig oder erstrahlen im ganzen Spektrum der Regenbogenfarben. Der Reise zur Vermählung mit dem Kleidungsstück steht nichts mehr im Weg.